Industry 4.0 – taking efficiency to new heights?
25.02.2019
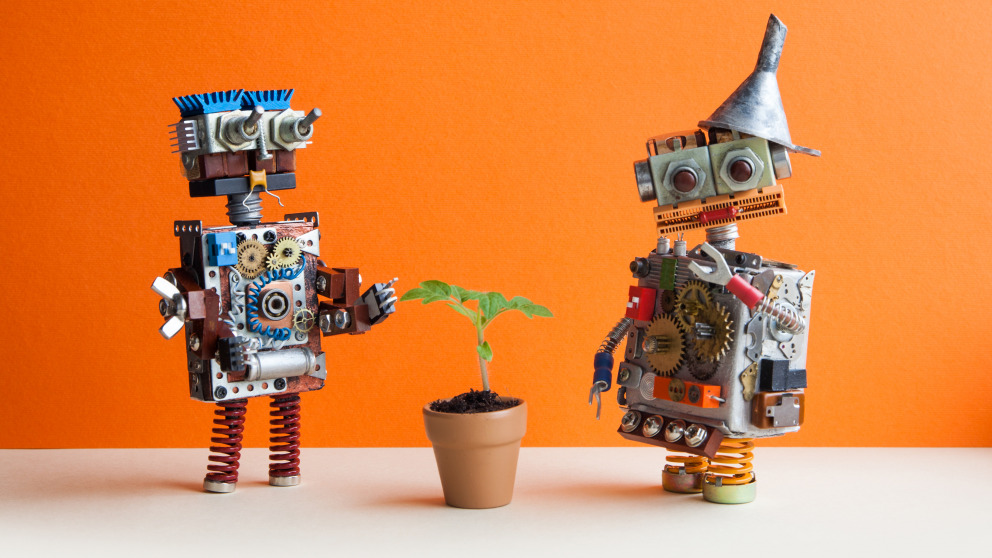
The industrial sector has a significant impact on global sustainability: According to the International Energy Agency, it accounted for 41.6% of global electricity consumption and 79.8% of global coal consumption in 2016. As socially responsible actors, manufacturers play an important role in the broader transformation towards sustainable development. This is particularly true of multinational corporations, many of which operate in countries with inadequate social and environmental standards. The digitalisation of industrial manufacturing processes cannot be separated from the debate on sustainable development.
The emergence of Industry 4.0 has been attended by expectations that its development would lead to substantial resource savings and greater resource efficiency – both abroad and in Germany (1). This article casts a critical eye on these expectations and considers the potential of Industry 4.0 to fulfil them, whether through gains in efficiency delivered by individual technologies or by enabling manufacturers to identify and exploit opportunities to save resources.
Resource savings potentials
Current research suggests that improvements in energy efficiency hold the greatest potential for resource savings. New software solutions can gather and aggregate data from across the production chain, providing greater transparency around energy consumption and enabling employees to schedule production to take advantage of shifts in electricity pricing. Another promising approach will exploit the flexibility of Industry 4.0 technologies to accelerate the deployment of renewable energy in manufacturing by scheduling production processes so that they track with peaks in the generation of energy from renewable sources. Efforts are also underway to improve the energy efficiency of industrial robots by optimizing the speed at which actions are carried out, rather than simply programming systems to work as quickly as possible. This approach could deliver energy savings of up to 30% (2). These aspects are particularly relevant in light of the rapid growth in the number of industrial robots and the increasing flexibility of production processes thanks to digital steering systems.
When it comes to material efficiency gains, the evidence is less clear. The use of modern technologies such as additive manufacturing (3-D printing) could certainly reduce material wastage. But in the near-term these products are unlikely to capture a significant share of the market and due to this the resulting material savings will not be significant.
The potential material savings are offset by the additional resources required to roll out Industry 4.0 in factories. This entails the retrofitting of manufacturing systems across the production chain with sensors, actuators, processors and communication technologies or indeed their replacement with modern systems capable of collecting and communicating relevant data. In addition to this, data from these systems is stored and processed on servers that require cooling – these already account for 2% of global electricity consumption (3).
Supporting corporate sustainability management
Sustainability management supports companies in their efforts to integrate the concept of sustainable development into their corporate culture, strategy, structures and processes. Creating transparency around corporate activities and decisions is a key aspect of sustainable corporate management. Enhancing external transparency, for example through sustainability reporting and auditing, can strengthen relationships with stakeholders and safeguard the reputation and credibility of a company.
Various scenarios for the implementation of Industry 4.0 also promise to improve transparency around production processes by connecting them across multiple levels and locations within a single company and even between different companies along the value chain, and in some cases over the entire life cycle of a product thanks to the use of data exchange technologies. These innovations hold considerable potential for corporate sustainability management.
Precisely how improvements in transparency can contribute to more effective sustainability management is the subject of multiple-disciplinary inquiry in the BMBF-funded Junior Research Group ProMUT (Transformative Potentials of Networked Manufacturing for Humans, the Environment and Technology). The project studies how data on the ecological impacts of products and processes can be fed into company software systems and how more flexible forms of production can be optimized to meet sustainability criteria such as greater resource efficiency. Identifying and engaging with stakeholders is a key part of this research and will ensure that the models of effective sustainability management developed through the project meet with acceptance.
From a social research perspective, the digital transition can also be studied in terms of the new channels of data and information exchange that are emerging both within and between organisations and their stakeholders. The digital transition will also leave its mark on globalisation as e-commerce opens up new opportunities for small and medium-sized companies. How this will affect indirect resource consumption levels (for example, relating to logistics) will need to be the subject of future study.
Conclusion
What can we conclude from the current state of research?
- There is a clear potential for digital technologies such as 3D-printing and optimized robotics to deliver energy and material savings. It is important to remember that Industry 4.0 is not a single technology, rather it is a concept in which different manufacturing technologies, information and communication technologies, and organizational aspects interact. Improvements in individual areas do not necessarily translate into net gains and we should be wary of drawing such conclusions. It will take systemic studies covering entire value chains to provide reliable estimates on the net effects in terms of energy and material savings. One possible starting point would be to examine the potential benefits that could be achieved through corporate sustainability management.
- There is some evidence to suggest that fully computerized manufacturing systems require more energy and raw materials than their conventional predecessors. This outcome is primarily due to the installation and operation of additional sensors, control units and data processing hardware.
Whether and to what extent the digital transition can reduce the ecological footprint of manufacturing is a matter of design. While potentials exist, it will take conscious efforts to deliver and tap into them.
Acknowledgement
The Junior Research Group ProMUT (BMBF Funding ID: 01UU1705A) is funded through the Social-Ecological Research Programme of the Federal Ministry of Education and Research.
Literature
(1) Beier, G.; Niehoff, S.; Xue, B. (2018): More Sustainability in Industry through Industrial Internet of Things? In: Applied Sciences, 8, 219, doi:10.3390/app8020219.
(2) Riazi, S.; Bengtsson, K.; Bischoff, R.; Aurnhammer, A.; Wigstrom, O.; Lennartson, B. (2016): Energy and peak-power optimization of existing time-optimal robot trajectories. In: 2016 IEEE International Conference on Automation Science and Engineering, pp. 321–327.
(3) Horner, N. C. (2016): Powering the Information Age: Metrics, Social Cost Optimization Strategies, and Indirect Effects Related to Data Center Energy Use. Dissertation 696.
This text is an abridged version of the German-language article “Effizienzwunder oder Ressourcenschleuder? Industrie 4.0. auf dem Prüfstand”, first published in politische ökologie (Bd. 155): "Smartopia. Geht Digitalisierung auch nachhaltig?“, oekom verlag München, December 2018, S. 64-69. www.oekom.de/zeitschriften/politische-oekologie.html