Making the Digital Transformation Deliver for Sustainability
11.05.2021
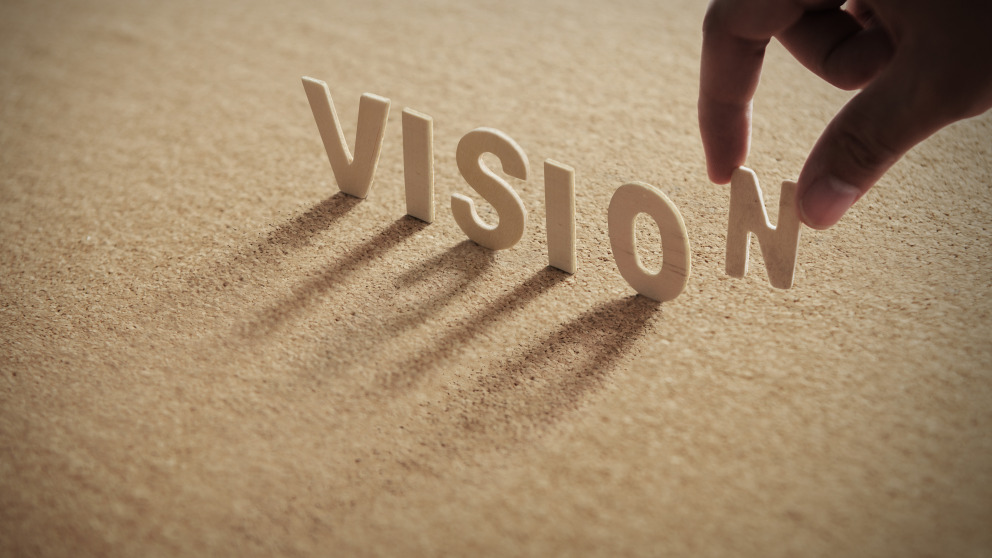
The digital transformation is in full swing, touching economies around the world. This far-reaching transformation is distinguished by three change processes affecting value creation models, information flows and resource flows – the latter two will be examined more closely in this post.
Changing information flows
Digital networks enhance information flows and potentially provide a means to consistently record the environmental impacts of business activities along the value chain and make them transparent – for management, external stakeholders and – not least of all – potential customers. The digitalization of corporate sustainability management processes could make an important contribution in this regard.
The adoption of digital technologies could improve the quality and availability of data at both the product and process levels, particularly with respect to materials and energy consumption. Big Data and artificial intelligence are among the more promising approaches here (Beier, Kiefer & Knopf 2020).
The creation and broad implementation of standards for the collection of data relating to sustainability management could also enable the comparison of environmental data across sectors and countries. Besides improving transparency, this would in turn facilitate the calculation of ecological footprints and consequently support the development of new resource-efficient products (Agez et al., 2020).
Changing resource flows
The paradigms of decarbonisation and dematerialisation play a central role in improving the sustainability of resource flows. Decarbonisation focuses on efforts to reduce the emission of gases harmful to the climate, such as CO2, in particular through the development of a sustainable energy supply based on renewable energy sources. Dematerialisation, on the other hand, is focused on producing goods and services with a minimum of material input, waste and emissions and, where this is unavoidable, utilizing materials or processes that are less harmful to the environment.
Implementing the Industry 4.0 concept in practice will entail the retrofitting of existing manufacturing systems across the production chain with sensors, actuators, processors and other communication technologies or indeed their replacement with modern systems capable of collecting and communicating relevant data. Considerable material and energy resources will have to be mobilized to make these industry-wide “upgrades” reality. But there are grounds for hope that the broad adoption of digital technologies across economies – and in industry in particular – will support the uptake of resource-friendly business practices that can increase efficiency and close resource cycles to build circular economies (Bag et al., 2021; Rajput & Singh, 2020).
Additive manufacturing is perhaps the most widely known approach to achieving material savings. It can also be used to produce lighter-weight products that in turn enable further efficiency gains in their use phase (Ford & Despeisse 2016; Dilberoglu et al. 2017; Rinaldi et al. 2020). The circular economy can only be adopted as a guiding economic principle if a systemic approach is taken and the entire product life cycle is considered. Efforts must be made during product development to ensure that products are made using recyclable and safe materials and with a modular design to facilitate their repairability or dismantlement. Digital Twins, based on non-proprietary and widely accepted data models, should be created for products, detailing the material inputs and assembly. These digital twins can then be used to support the recycling, upcycling and reverse logistics processes crucial to a future circular economy.
These activities should be flanked by the establishment of digital platforms that enable user-friendly B2B brokerage and trading in secondary raw materials. The electronic product passport currently being developed in the EU could be a good starting point for this. There is also a need for open data spaces where the public can access information on best practice approaches to material reuse and design for disassembly, as well as other relevant findings from publicly funded projects. These efforts could help to connect and integrate the flow of materials between different industry sectors through digital technologies.
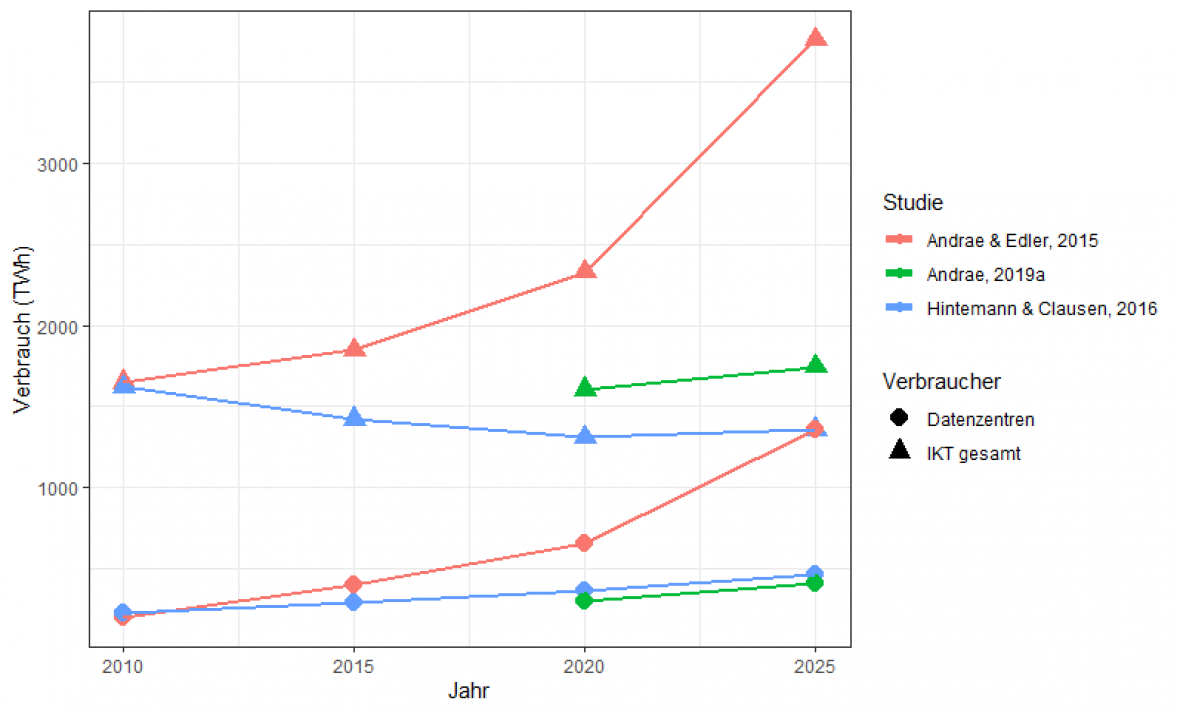
Figure 1: Anticipated energy requirements of ICT and data centres
An increasingly digitalized economy will require a lot of energy. As Figure 1 shows, some studies forecast an (slight) increase in energy demand for ICT applications globally over the near term (Andrae & Edler, 2015; Andrae, 2019; Hintemann & Clausen, 2016).
On the other hand, interesting opportunities to improve energy efficiency exist at the process level. Digitalization can also help to optimize energy efficiency in production processes. Efforts are underway to optimize the energy consumption of industrial robots, for example, by improving the efficiency of their motions, rather than simply programming systems to work as quickly as possible. This approach has delivered energy savings of up to 30% in one automotive use case (Riazi et al., 2016).
The digitalization of the economy also holds opportunities to facilitate ecological industrial symbiosis. The widespread integration of the economy – sometimes referred to as sector coupling – is desirable in the long term in order to achieve optimize energy consumption and efficiencies across different industries. In order to increase the share of renewable energy in total energy consumption and cushion fluctuations in its generation, digital technologies will need to be used to support sector coupling, making industry an active player in the decentralised energy management. One promising approach exploits the flexibility of Industry 4.0 technologies to accelerate the deployment of renewable energy in manufacturing by scheduling production processes so that they track with peaks in the generation of energy from renewable sources. (Ma et al. 2020; Faheem et al. 2018).
Conclusions
Research has yet to confirm whether such approaches can in fact compensate for the additional demand for raw materials and energy required for the manufacturing and operation of digital technologies (Niehoff & Beier, 2018). Studies show that while transitioning to Industry 4.0 production processes is likely to result in efficiency gains, but that in many cases this will not translate into significant reductions in material and energy consumption (Fritzsche, Niehoff & Beier 2018). This is due to an absolute increase in production, a tendency to focus exclusively on process efficiency, and a failure to exploit the potential of digitalisation for corporate environmental management (Beier, Kiefer & Knopf 2020).
However, there are indications that, used judiciously, digitalisation can indeed achieve positive ecological effects. Realizing potentials and preventing negative rebound effects requires adequate incentives and regulatory frameworks and the backing of political actors.
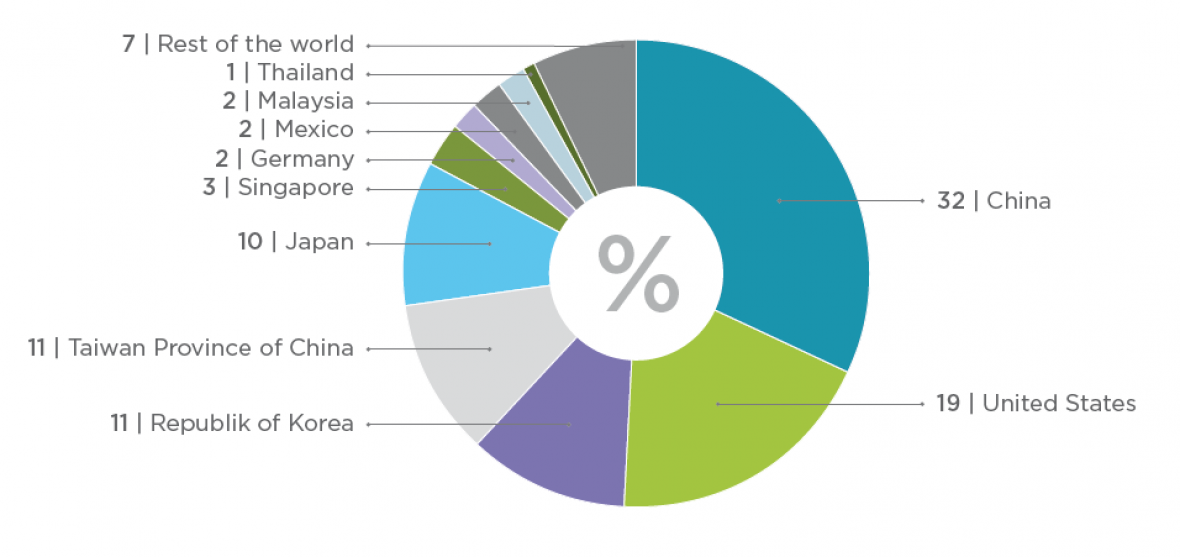
Figure 2: Geographic distribution of value added in ICT manufacturing [in %] in 2017, based on UNCTAD (2019)
Many of the raw materials used in the production of digital devices, which are predominantly used in the Global North, are mined in the countries of the Global South – with significant negative impacts for people and the environment. There is an urgent need to ensure that digitalisation does not exacerbate existing imbalances between the Global North and South.
We cannot afford to simply trust that companies and consumers will pursue digitalisation in a way that is compatible with the goals of protecting the environment and climate. Instead, we need intelligent political and regulatory frameworks to make the digital transformation a sustainable one. If digitalisation is to serve the common good, it must be guided by the overarching goal of promoting development pathways that are more sustainable in the economic, environmental, and social dimensions.
In order to adequately resolve the conflicts and dilemmas that will inevitably arise during this transformation, the relevant actors must engage in a mutual process of co-designing objectives, rules and regulations for a governance structure in line with the normative goals of sustainability (Renn, Beier & Schweizer 2021). If we wish to create a sustainable digitalised economy, we will need to put the well-being of people and the environment at the centre of national and international debate and ensure that the digital transformation is guided every step of the way by the United Nations Sustainable Development Goals.
Literature
Agez, M., Wood, R., Margni, M., Strømman, A. H., Samson, R. & Majeau‐Bettez, G (2020). Hybridization of complete PLCA and MRIO databases for a comprehensive product system coverage. Journal of Industrial Ecology.
Andrae, A. S. G. & Edler, T. (2015). On global electricity usage of com-munication technology: trends to 2030. Challenges, 6(1), 117–157.
Andrae, A. S. G. (2019a). Comparison of Several Simplistic High-Level Approaches for Estimating the Global Energy and Electricity Use of ICT Networks and Data Centers. International Journal, 5, 51.
Bag, S., Yadav, G., Dhamija, P. & Kataria, K. K. (2021). Key resources for industry 4.0 adoption and its effect on sustainable production and circular economy: An empirical study. Journal of Cleaner Production 281, 125233.
Beier, G., Kiefer, J. & Knopf, J. (2020). Potentials of big data for corporate environmental management: A case study from the German automotive industry. Journal of Industrial Ecology 57 (8), 1883.
Dilberoglu, U. M.; Gharehpapagh, B.; Yaman, U. & Dolen, M. (2017). The role of additive manufacturing in the era of industry 4.0. Procedia Manufacturing, 11, pp. 545–554.
Faheem, M.; Shah, S.B.H.; Butt, R. A.; Raza, B.; Anwar, M.; Ashraf, M. W.; Ngadi, Md.A. & Gungor, V.C. (2018). Smart grid communication and information technologies in the perspective of industry 4.0: Opportunities and challenges. Computer Science Review, 30, 1–30.
Fritzsche, K.; Niehoff, S. & Beier, G. ( 2018). Industry 4.0 and climate change—Exploring the science-policy gap. Sustainability, 10 (12), 4511.
Ford, S. & Despeisse, M. (2016): Additive manufacturing and sustainability: an exploratory study of the advantages and challenges. In: Journal of Cleaner Production 137. pp. 1573-1587.
Hintemann, R. & Clausen, J. (Eds.). 2016. Green Cloud? The current and future development of energy consumption by data centers, networks and end-user devices: Atlantis Press.
Ma, S.; Zhang, Y.; Liu, Y.; Yang, H.; Lv, J. & Ren, S. .(2020). Data-driven sustainable intelligent manufacturing based on demand response for energy-intensive industries. Journal of Cleaner Production, 274,123155.
Niehoff, S. & Beier, G. (2018): Industrie 4.0 and a sustainable development: A short study on the perception and expectations of experts in Germany. In: International Journal of Innovation and Sustainable Development, Special issue on Advances in Green Economy and Sustainability 12 (3), pp. 360-374.
Rajput, S. & Singh, S. P. (2020). Industry 4.0 Model for circular economy and cleaner production. Journal of Cleaner Production 277, 123853.
Renn, O.; Beier, G. & Schweizer, P.-J. (2021). The opportunities and risks of digitalisation for sustainable development: a systemic perspective. GAIA – Ecological Perspectives for Science and Society; 30:23–8. Doi: 10.14512/gaia.30.1.6.
Riazi, S., Bengtsson, K., Bischoff, R., Aurnhammer, A., Wigström, O. & Lennartson, B. (2016). Energy and peak-power optimization of existing time-optimal robot trajectories. In 2016 IEEE International Conference on Automation Science and Engineering (CASE) (pp. 321–327).
Rinaldi, M.; Caterino, M.; Fera, M.; Manco, P. & Macchiaroli, R. (2020). Technology selection in green supply chains – the effects of additive and traditional manufacturing. Journal of Cleaner Production, 124554.
UNCTAD ( 2019). Digital Economy Report 2019: Value Creation and Capture: Implications for Developing Countries. https://unctad.org/en/PublicationsLibrary/der2019_en.pdf.
This blog post was first published on 21 April 2021 on the „inclusive productivity“-Blog.